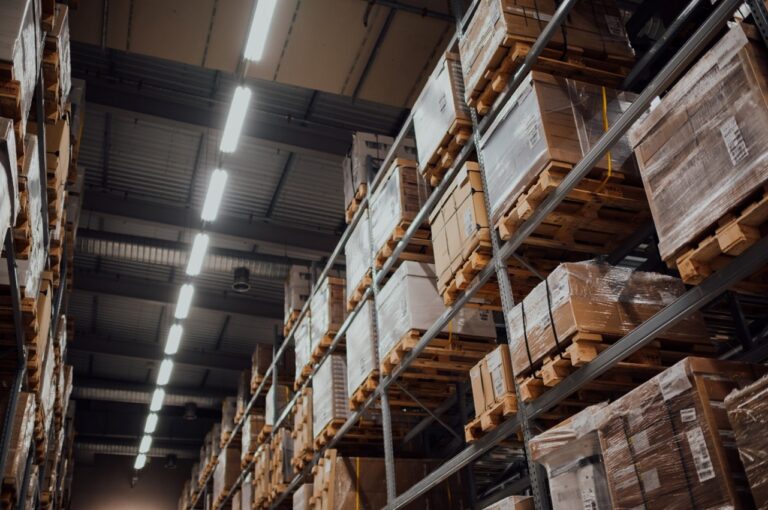
Due to an increasing level of supply chain disruptions, there has been a growing pressure for distribution centers to perform more efficiently and optimally than ever. The shift to 24/7 operations meant these facilities would need to hire more staff to process greater volumes, all while striving for maximum uptime. As little as a few hours of downtime can cause a domino effect. If even one critical machine part fails, the entire distribution center may have to halt operations leaving hundreds of employees sitting idle.
How can distribution centers maintain high performance while keeping downtime at a minimum? It largely comes down to two things: predictive maintenance and a well-trained team. If team members can actively detect and prevent machine failures before they occur, distribution centers can handle even historic volumes of product.
Purchase Crucial Spare Parts Before They’re Needed
Reactive, just-in-time inventory practices associated with lean operations can result in chaos when most suppliers are battling lengthy backlogs for parts and service. Look for opportunities to stockpile what you need and if your parts inventory is low, order now. Standardizing your equipment can also help alleviate supply issues. Instead of using 25 different types of motors, you might be able to use 15 – a reduction that can make it easier to stock replacements. If you want to get a better idea of when a part like a bearing would need to be replaced, you can invest in condition monitoring equipment such as UE System’s Ultraprobe 15,000. Typically used on sorters, crossdocks, and singulators, this ultrasonic listening device can detect bearing friction and determine when a failure and replacement may be imminent.
Employ Condition Monitoring Devices
Though an important and crucial part of any maintenance strategy, visual inspections and manual processes are no longer entirely effective on their own when facilities are running 23 or 24 hours per day. One of the most challenging aspects of manual inspections is accessibility to critical equipment due to safety and hard-to-reach locations. To eliminate safety risk while also reducing the amount of time it takes to collect data on hard-to-reach assets, you can install remote access sensors (RAS) in key areas around your facility. Simply mount the RAS sensor on the test point and run a cable to a more accessible area where a remote access module can be connected, immediately simplifying the process of testing in hard-to-reach areas. With the RAS sensor in place, you are now able to collect more accurate and consistent ultrasound readings in a safer, more accessible manner.
Investing in a combination of ultrasound technology, oil analysis tools, and even vibration sensors can give you an inside look at your equipment and predict lifecycles of critical parts. With any new technology, ensuring your staff is properly trained in using condition monitoring tools to their full advantage is necessary. By collecting data and using it to drive decisions, your team can effectively keep downtime at a minimum.
Invest in a Training Plan for Employees
You can have the nicest technology, machinery, and facility on the map, but your productivity will continue to suffer if your employees aren’t trained on the more complex systems needed to handle the volumes distribution centers are being called on to process. Continuous operation requires different, and often more advanced skills to keep these centers running at optimal levels. In a constrained labor market, finding these sought-after maintenance professionals can be a challenge. Now is the time to invest in training for long-term members of your maintenance team.
The heightened number of supply chain disruptions combined with the dramatic shift to e-commerce will continue to influence distribution center operations as we know it, requiring those who manage operations and maintain equipment to remain flexible and vigilant. In the new era of distribution center maintenance that’s unfolding before us, it’s never been more important to focus on the crucial role of predictive maintenance and life-cycle monitoring.