by UE Systems, Inc.
Partial Discharge are a very serious problem. When electrical equipment fails, it can cause large periods of unplanned downtime and even be a life-threatening hazard to the personnel working at an industrial facility.
Typical tools used by maintenance teams to detect partial discharges include infrared cameras and ultrasonic inspection instruments. These are effective tools, but both have some limitations: infrared cameras will only work when heat is present (thus, it can’t detect partial discharge types such as corona) and ultrasonic inspection instruments are typically listen-only and require sound recording and spectrum analysis to diagnose the type and severity of the partial discharge.
The role of Ultrasound in Detecting Electrical Equipment Failure
Arcing, tracking, and corona emissions produce ionization, which is a process by which a neutral atom or molecule loses or gains electrons, thereby acquiring a net charge and becoming an ion; occurs as the result of the dissociation of the atoms of a molecule in solution or of a gas in an electric field. Ionization has by-products: ozone and nitrogen oxides. These combine with moisture to produce nitric acid, which is destructive to most dialectics and certain metallic compositions, resulting in corrosion.
The objective of electric condition monitoring is to detect the presence of these events before flashover occurs or before they produce an arc flash incident when a cabinet is opened.
Ultrasound technology is ideally suited for detecting these emissions since the ionization process produces ultrasound. The typical ultrasonic instruments sense between 20-100 kHz and use heterodyning to translate these ultrasonic emissions into the audible range.
However, there may be instances where it is difficult to determine the type of problem heard through the headphones. In these situations, a sound recording of the condition can be made (some instruments have on-board sound recording capability) and viewed on spectral analysis software. The sounds may be heard in real time as they are viewed on an FFT or time series screen for analysis. This enables inspectors to observe subtle problems that might be missed by just viewing a screen without sound.
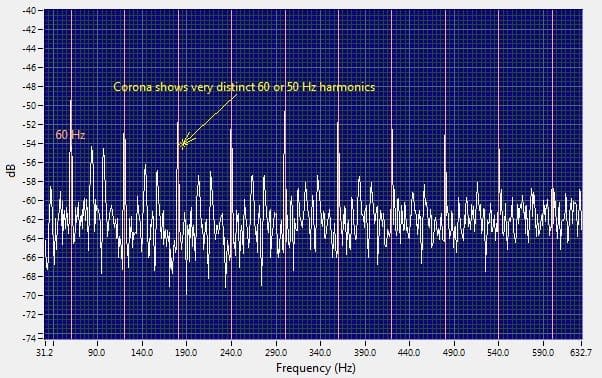
Picture 1 – Corona, as seen on a sound spectral analysis software. This type of partial discharge will show clear harmonics at 60 Hz (USA) or 50 Hz (Europe).
One Step Further: Using Ultrasound Cameras to Detect Partial Discharges
Recently, the development of ultrasound cameras has made detecting partial discharges easier than ever. These cameras are amazing tools – they offer an effective visual inspection, just like infrared cameras, while also offering the primary advantages of ultrasound when it comes to electrical inspections: the ability to pinpoint failures even when heat is not present (like, for example, Corona).
By being this effective in detecting partial discharges, these cameras can lead to significant savings by avoiding expensive downtime while simultaneously guaranteeing the invaluable safety of personnel.
When using an ultrasound camera, electrical failures such as corona, tracking, and arcing are easily detected. By simply pointing the camera at an electrical asset, the inspector will see any partial discharge locations shown on the screen. Some ultrasound cameras can even clearly distinguish partial discharges from other ultrasound sources, reducing the number of false positives, and thus making inspections much more effective. These cameras are a true game changer when it comes to finding partial discharges.
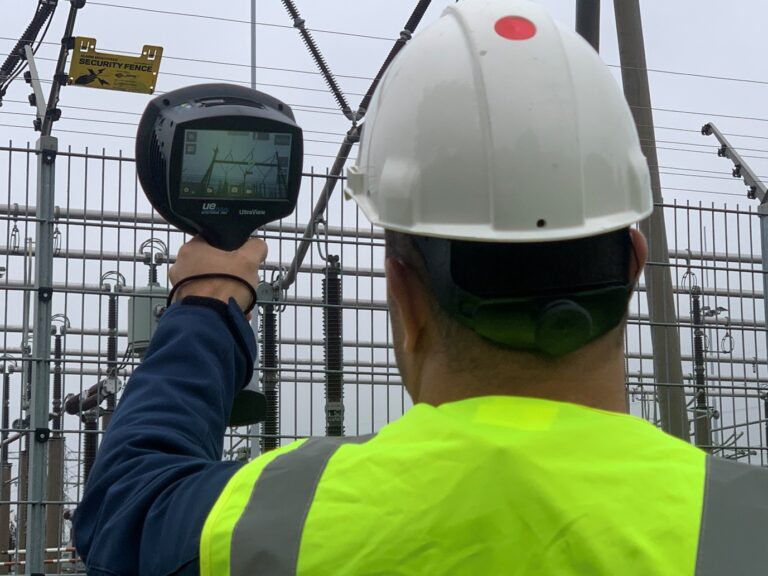
Picture 2 – Ultrasound camera used to detect partial discharge at an electrical substation.
Normally, an ultrasound camera will be ready to use right out of the box – its operation requires minimal training and partial discharges can be detected without the need for any additional software installation.
Quick Diagnostic: Easily Assessing Partial Discharge Type and Severity
By using an ultrasound camera, with a little help from AI, an inspector can get a quick assessment of the partial discharge type and its severity, as well as a suggestion for corrective actions. This can be extremely handy by helping maintenance teams prioritize their work, and it’s also a significant time saver since there is no need to analyze the sound file on a dedicated software. However, cameras such as the UltraView Ultrasonic Camera from UE Systems still allow for sound recordings in case the inspector wants to dig deeper into the issue and get a more robust diagnostic using a sound spectrum analysis software.
The UltraView Camera provides an unparalleled level of intelligence, enabling inspectors to swiftly detect partial discharges and evaluate the intensity with 10x more efficiency than conventional inspection methods. Since all partial discharge locations are displayed on the screen in real-time, inspectors can quickly save thousands of dollars in repairs and unplanned downtime.
Cameras such as the UltraView will also quickly generate PDF reports on all detected partial discharges.
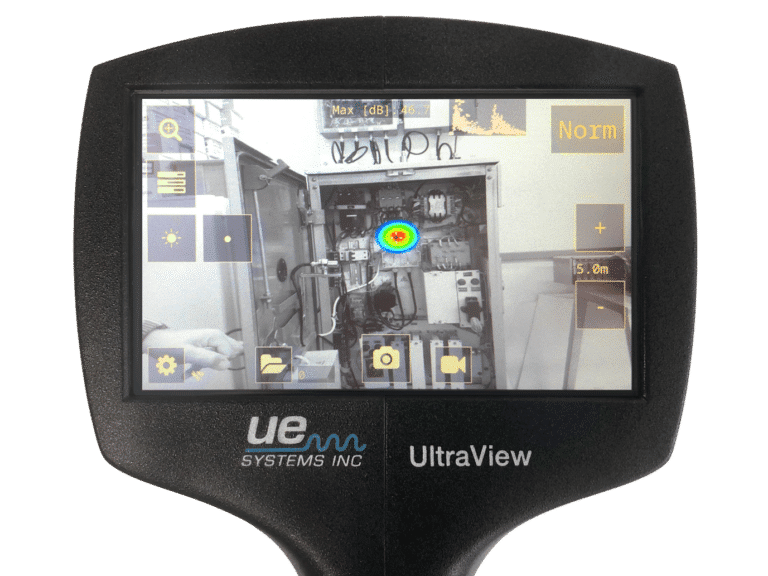
Picture 3 – Ultrasound camera detecting a partial discharge. Notice the spectrogram on the top right, which only shows up when the sound source corresponds to a partial discharge.
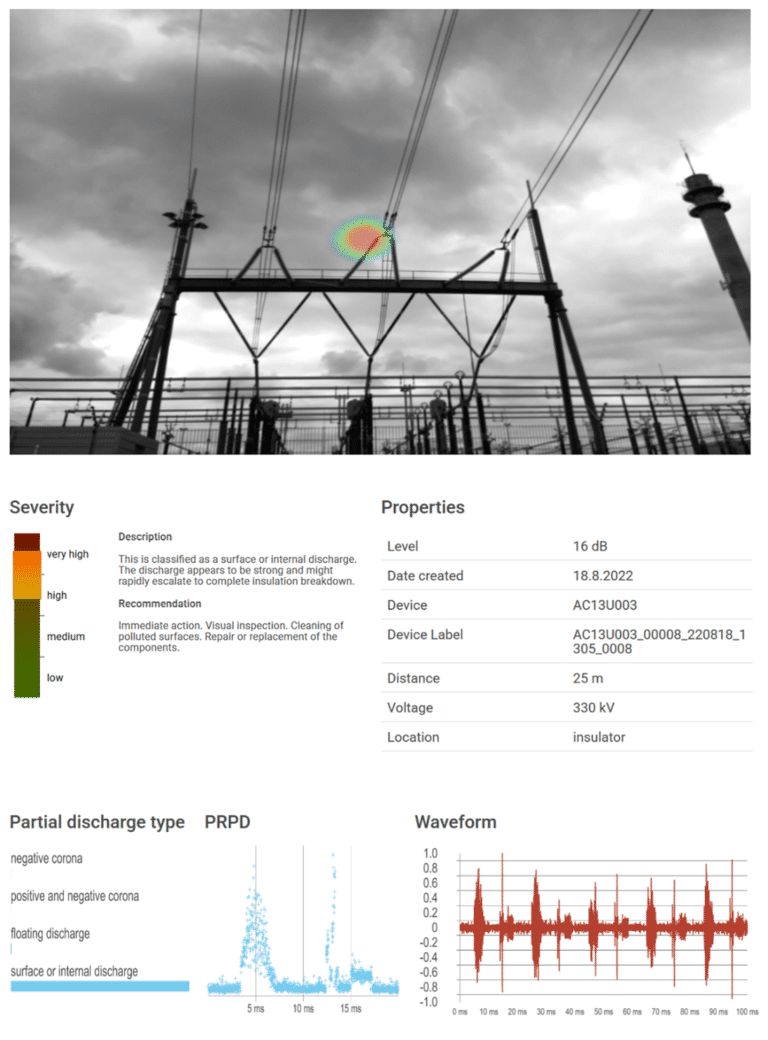
Picture 4 – Snapshots of a partial discharge detected by the UltraView Camera. You can see the amount of useful information the inspector will get on the spot.
Conclusion
While infrared cameras and the typical listen-only ultrasonic instruments are still very valid tools for partial discharge detection, they can’t compete with a proper ultrasound camera when it comes to speed of detection, effectiveness, and ease of diagnosis and report generation. Ultrasound cameras are, without a doubt, a significant upgrade when it comes to finding electrical issues. Considering that most of these devices are also capable of detecting air leaks, an ultrasound camera is the no brainer solution when it comes to providing a quick ROI.